The product
The product is a programmable logic controller (PLC), a compact dedicated computer for industrial applications. It is used for automation of processes and provides extended controls for machines and its parameters. Users vary from Electrical, Maintenance engineers to wiremen and shop floor workers. It is used by companies to automate processes and bring in reliability, efficiency and reduce human errors in machine usage. Some applications include Production monitoring systems, Equipment testing jigs, etc. This device connects to various other devices like sensors, switches, motors etc. to communicate and control them. It is programmable to perform checks and send required signals to control and run processes. This product is a vital part of any modern shop floor.
The Challenge
As a finding from the user and field research, strong competition and crowded market demanded a very strong perceived quality for the product. Our challenge was to build it through a robust design make it simple to use and clutter free. The product works in an industrial environment with high demands on performance and functionality. The focus was on creating a simple, usable, clean yet a reliable product.
One of the biggest challenges was ease of wiring and user safety. The old design used an exposed connector with each module having about 20 connections. Making the connections was tedious. Trouble shooting and diagnostics was even more difficult. Accidental contact with live wire was common. A better solution for safe handling of wires during installation was highly needed.
Simplify Modularity in the product. Often a customer adds on modules as and when his need arises. Addition of modules was difficult and causes a significant downtime. This modularity was not easy to handle at the user level. The PCBs would be exposed and lead to product damage while handling.
Enhance user feedback for diagnosis, installation and servicing. The electronics (PCBs) of the current design was a constraint, could not be changed as they had already been tested on the previous design cycle. The challenge was to enhance diagnostic assistance in an ergonomic intuitive manner. Overall the objective was to create a product which would be easy to wire, safe to handle, provide ease of diagnostics and be distinct in styling to create differentiation in the market.
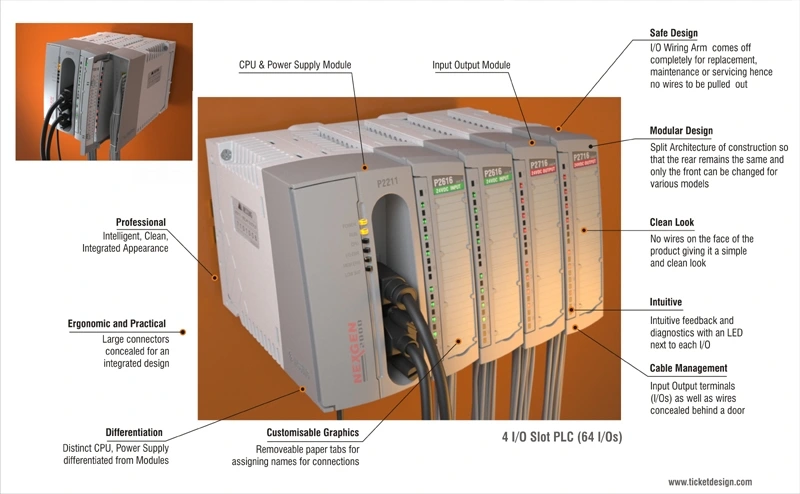
The Process
To ensure the most effective design solution, Ticket Design conducted extensive study with end users, control panel builders to understand their needs and requirements. From these studies, the interface, product packaging and feature parameters were explored and defined, establishing the foundation for preliminary concepts and sketches. The result was a product that is useful for the end users as well as the technicians and installation engineers.
The Benefits
The redesigned product is a clean, safe and simple design with enhanced ergonomics. The modular product has a new removable front wiring module that takes the complexity out of wiring a PLC. All the wiring can be done separately and PLC assembled later on. Diagnostics now can be done without complicated rewiring. The product now has no exposed connectors or wires; no accidental shocks any more. The product styling has been carefully worked out to position the product as an intelligent, contemporary and a differentiated product in the market. The product has been designed for an international market using engineering plastics and uses latest technologies of injection moulding mass production to achieve economy of scale.
Ergonomics: Modules can be easily replaced and removed. A unique front wiring module can be removed without touching a single wire.
Modularity The product is modular and expands depending upon the requirements of connections upto 128 input/outputs.
The product is being rolled out and the sales are expected to double this year.